Lean and quality thinking are a good start, but...
Lean and quality are usually employed to further success by classic expansionary thinking -- higher revenue, better margin, more growth. See the "Details" view.
- Lean thinking defines waste as what customers would not pay for if they knew about it. This presumes minimizing cost to satisfy more customers with higher quality, good so far. But it ignores other stakeholders. And if customers will pay for it, who needs to be concerned with waste?
- In practice, most kaizen is on already established processes. Had more thought gone into these when they were first designed, much waste could have been avoided. (If a product is poorly designed to be built or serviced, improving the processes to make or service them hits limits.) This kind of thinking has to project further into the future. And it has to encompass a full life cycle of performance. Quality is never a "now-we-can-forget-it" attribute.
- Lean and quality thinking usually wage a never-ending battle with financial models and accounting systems. Lean and quality tend to look at what we really do. Financial systems look mostly at outcomes, and they do not, of themselves, investigate what could be done differently.
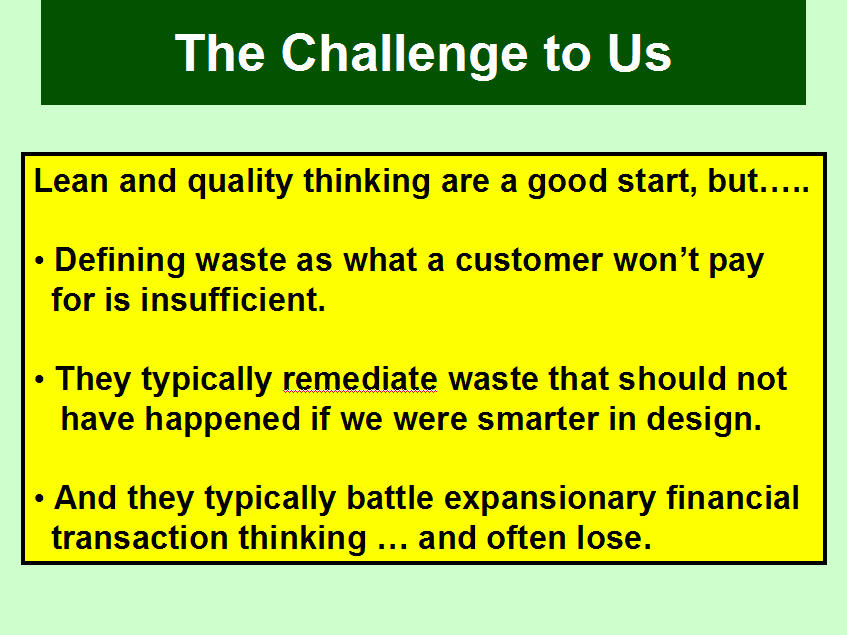